Our expertise
Thibault and his team have traditional jewelery know-how known as "à la française", combined with a perfect mastery of new technologies such as 3d modeling and 3d printing.
Passionate about their profession, they put the same level of standards and the same attention to detail into each jewel they make.
Here are the different stages in the production of a Thibault jewel:
- Creation of the jewel: this is the first step in the manufacture of a jewel where you have to define the shape, the style of the jewel, then the nature, the shape and the number of stones that will adorn it.
- 3d modeling: from this stage we concretely build the jewel using computer software called "NURBS modeler" which allows the jewel to be drawn in 3 dimensions.
- 3d printing: once the jewel has been modeled, we will print it in resin.
- Lost wax casting: once the jewel is 3d printed, we will melt it using the lost wax casting technique. For this we will mount the resin on a wax rod that we will place in a cylinder made of plaster. We are going to bake the cylinder at around 700°C, the wax will melt and leave an imprint in the plaster cylinder. In place of this imprint we will cast the metal (gold, silver or platinum).
- Cast remediation and assembly: Once the metal cast is released from the plaster cylinder, its surface is grainy. Using emery paper, we proceed to "melting recovery", that is to say that we remove this grainy surface in order to prepare the surface of the jewel to be perfectly polished. Once this step has been completed, if the jewel is in several parts, they can be adjusted and assembled together.
- Welding: if the jewel is in several parts, we can weld them together after adjusting them. We generally use a torch and solder which melts at a temperature lower than that of the jewel to prevent the entire setting from melting during this step.
- Pre-polishing: this is a step that we generally use in fine jewelry, which consists of polishing the parts below the stones that will no longer be accessible once they are set on the jewel. The metal underneath the stones will shine brightly and enhance their beauty.
- Setting: this is a delicate manufacturing step that consists of setting the stones in the metal. There are a multitude of types of setting such as the grain setting, the claw setting, the closed and semi-closed setting, the Parisian nail, invisible setting...
A good setter needs many years of experience to feel and know how to bend the metal on the stone without breaking it.
- Polishing: this is one of the final stages that totally magnifies the jewel. Using cotton discs inserted on a polishing drum that can rotate up to 10,000 revolutions per minute and polishing paste, he will caress the jewel to make it shine with a thousand lights, we call this type of polishing " mirror polished".
- Rhodium plating: this is a plating technique carried out by electrolysis, otherwise known as "electroplating", which consists of depositing a sheet of rhodium on metals. Rhodium is a very white and very hard metal which gives white gold a white appearance.
TRIBUTES:
- Ankle work: in our jargon we say that jewelers work "ankle".Today it is a piece of wood that is attached to our workbench and that we rely on to work on, but in ancient Egyptian times jewelers actually worked on their dowel
- Lost wax casting: Lost wax casting is a technique that was already used in Ancient Egypt, more than 2000 years ago!
Today, artisan jewelers can use cuttlebone to melt jewelry. Simply cut the cuttlebone in half, make an imprint of what you want to melt in the very friable inner part of the bone. Then we remove the object taken as an impression and we make a small "chimney" to be able to pour the metal. Both sides are closed and the molten metal can be poured. It is an artisanal and approximate technique which is not used by professional founders
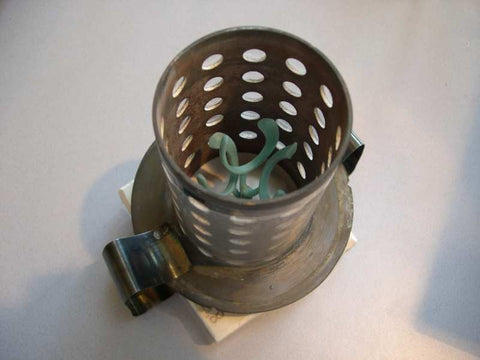
- Fly: this is a ribbon of emery paper that is wrapped around a mandrel which, in rotation, catches up the cast iron. The sound it makes in contact with metal sounds like a fly
- Doll: when the setters work on certain types of setting, they are sometimes dazzled by the twinkling of the stones. They then put talc on the set part to obstruct the sparkle of the stones. For this they use a piece of cloth in which is enclosed talc which they tap on the part to be blocked. This little piece of fabric looks like a doll
- Workbench skin: traditionally we use a leather skin installed below the peg of the workbench which makes it possible to recover metal filings and thus avoid losing them. This flexible skin also allows you to catch stones and prevent them from breaking when falling on the ground.
- Filing boxes: the precious metal filings that we recover from this famous skin are then stored in filing boxes. Each jeweler has their own boxes. In our jargon we call jewelers filing boxes.